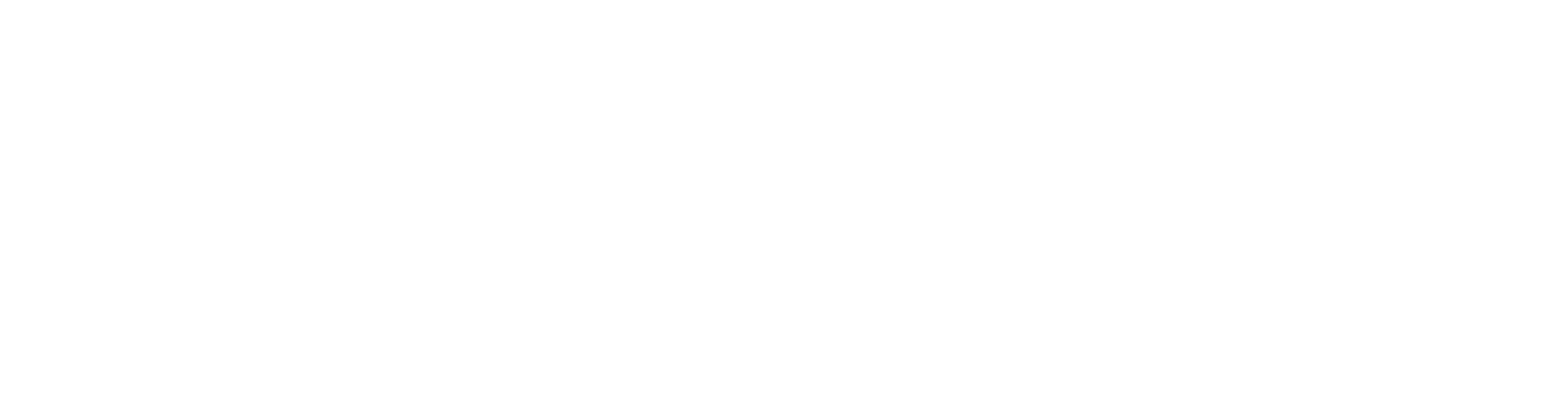
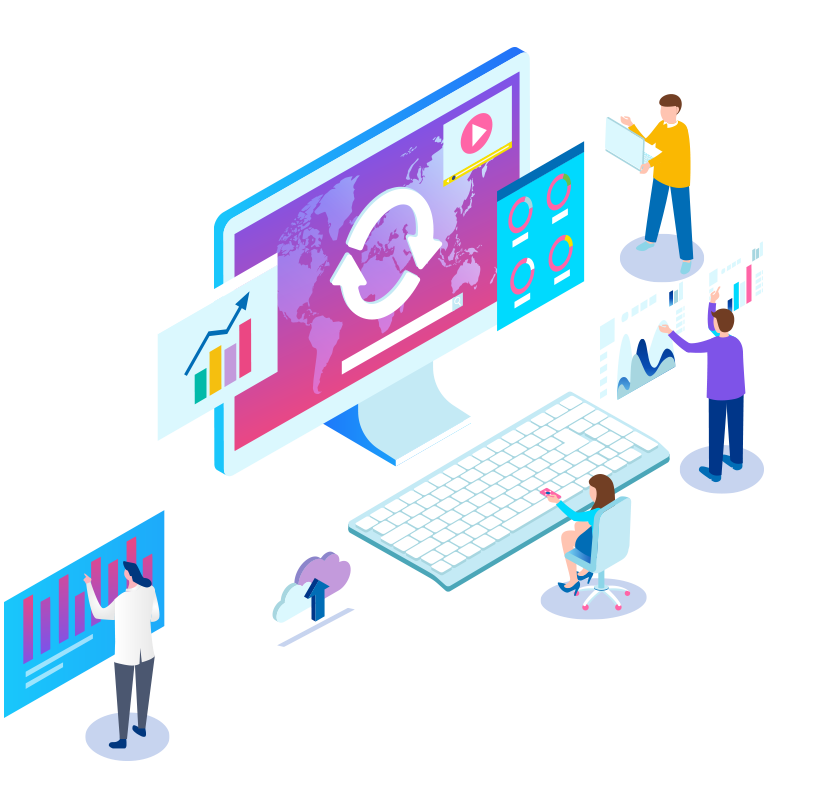
and capabilities for the ocean and logistics supply chain.
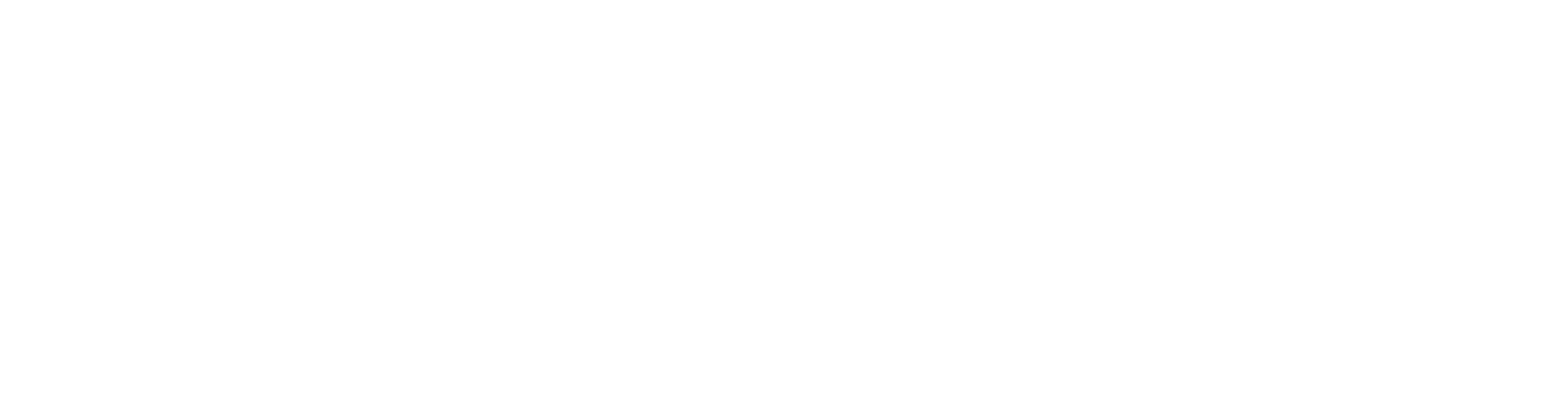
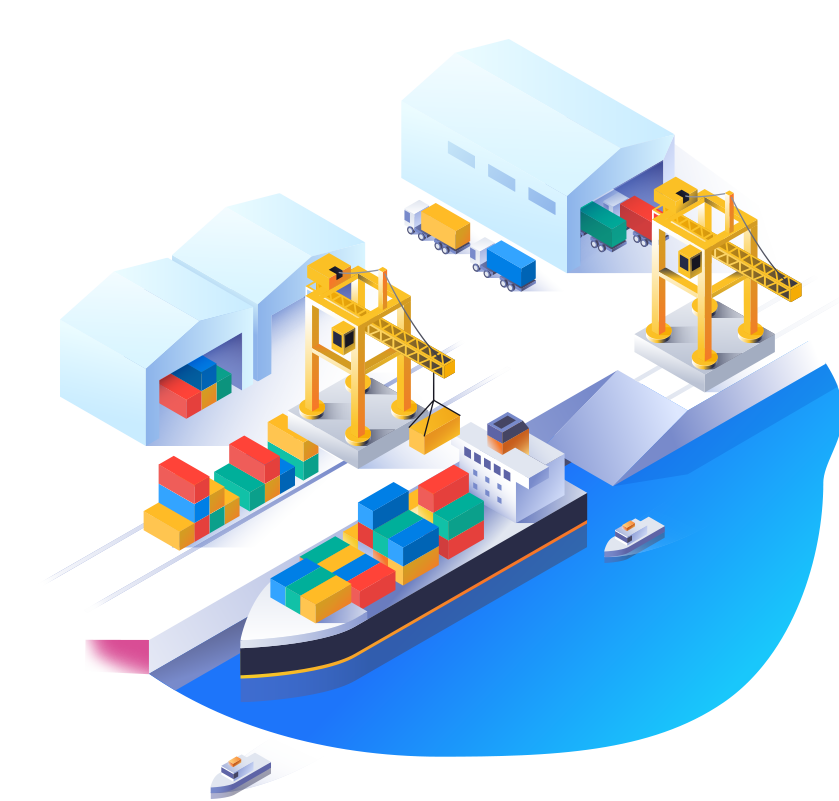
digital transformation successfully.
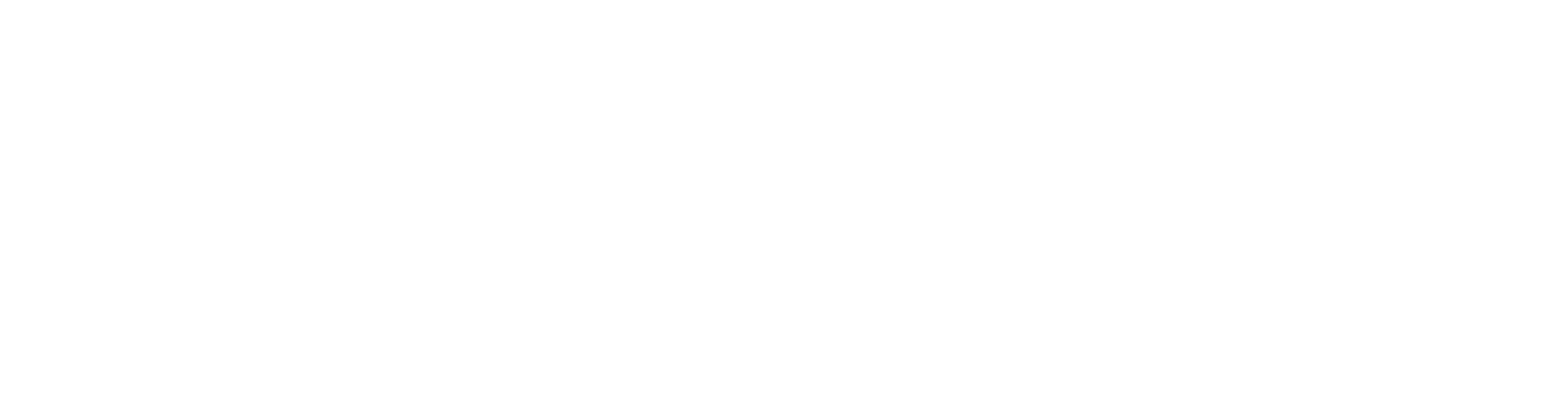
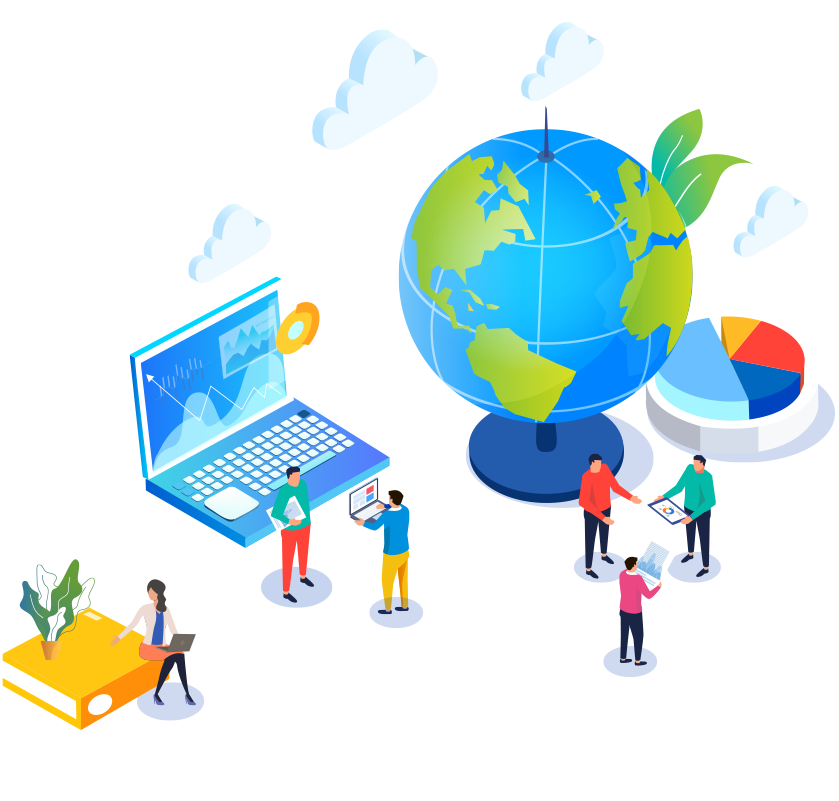
and driving progress toward a sustainable future with
eco-friendly energy and future technology business.
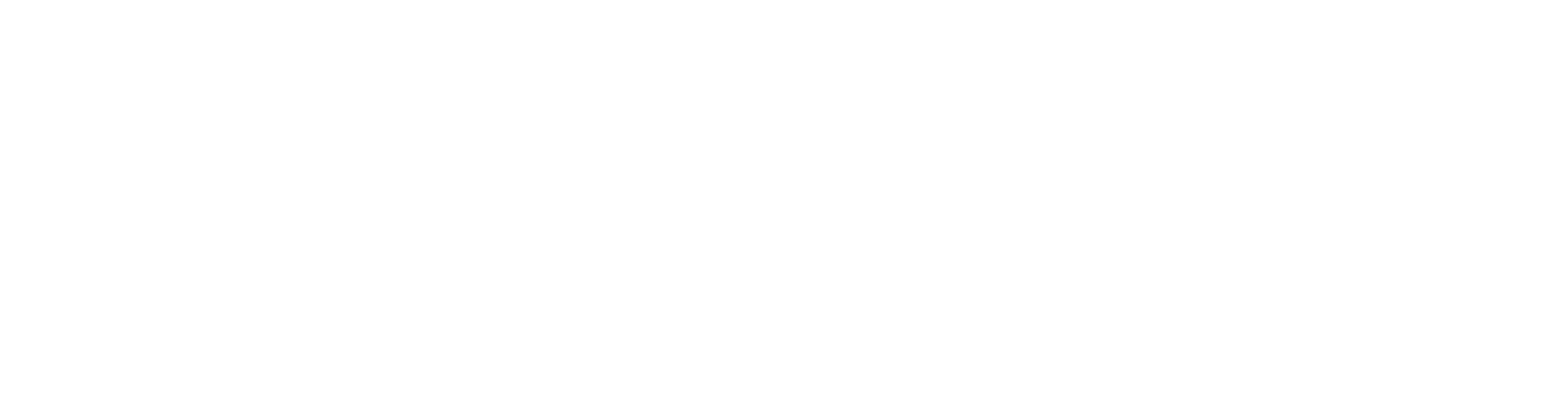
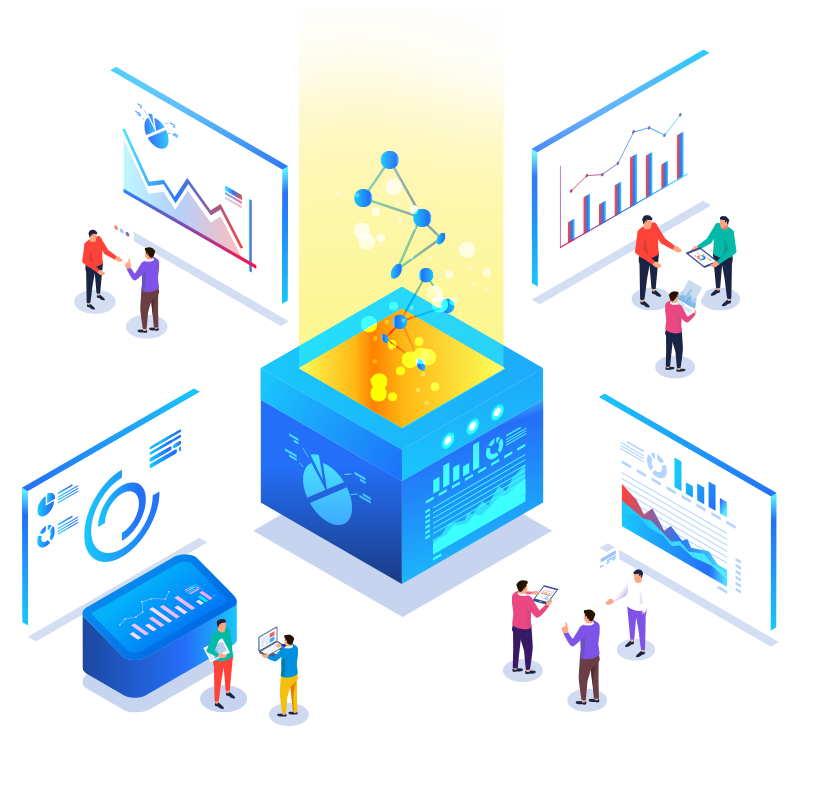
technologies based on big data.
About CLT
CLT provides digital transformations to the global logistics industry, based on innovative technologies. CLT globally leads the logistics industry, including shipping and port industries, by solving the global supply chain’s operational challenges and improving visibility through innovative technologies, enabling us to respond quickly to rapidly changing market demands. We provide consulting services and flexibly scalable solutions that span all industries.
-
22+ Years
-
700+ Employees
-
15+ Shipping Companies
-
36+ Terminals
-
140+ Logistics Companies
-
30+ Countries

SOLUTION INFORMATION
CLT, for more than 20 years as the partner of many shipping companies, terminals, and logistics stakeholders, we provide the platform for optimizing business activities, applying the latest processes, and integrating them. We are constantly working to develop the tools that enhance business automation, communication, and collaboration to increase our clients' work efficiency, strengthen competitiveness, improving productivity and service quality.
Maritime
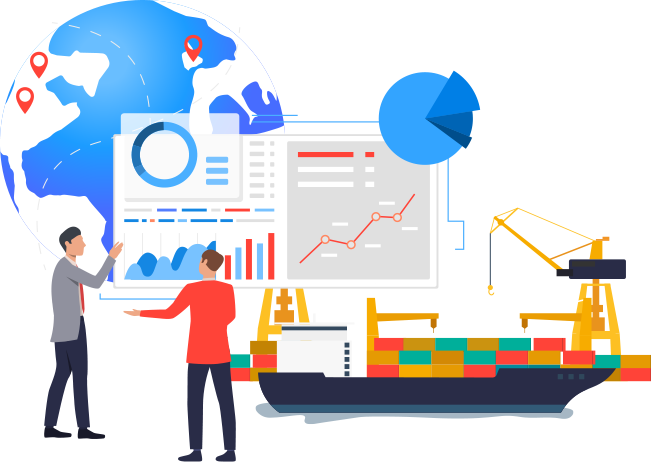
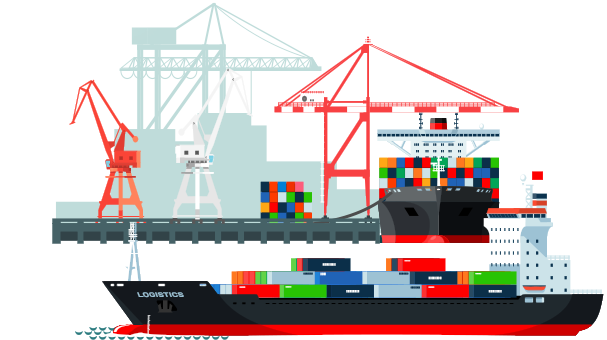
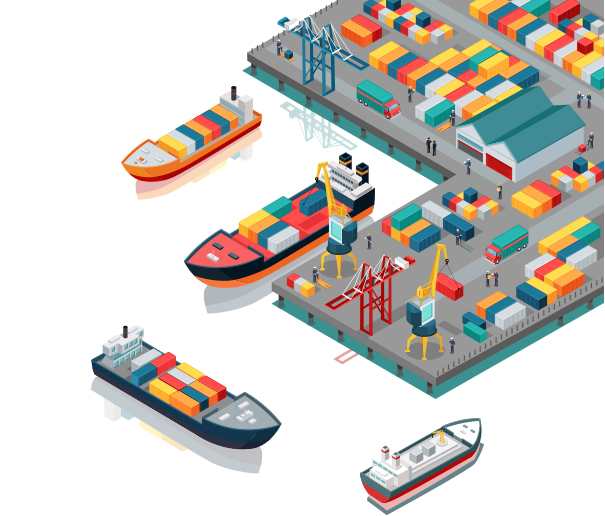
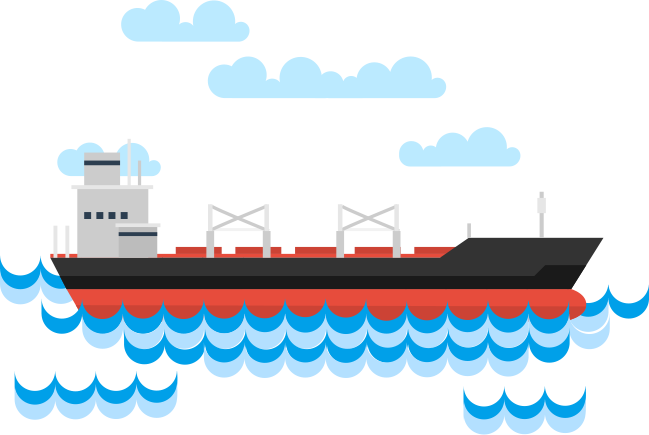
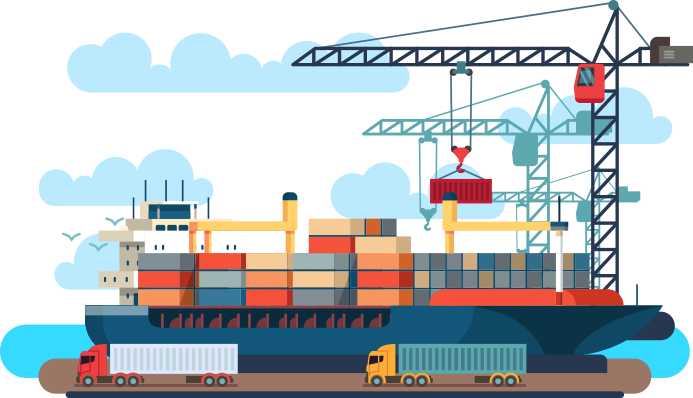
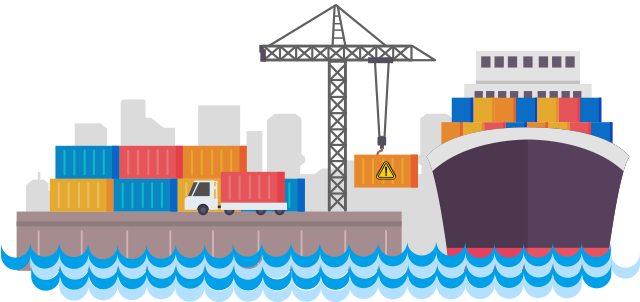
- ALLEGRO
-
Container Shipping Liner Solution
ALLEGRO is the solution for integrated shipping operations that supports digital transformation, including adopting the latest operation, system and process in line with the increasing competitiveness of service and dynamically changing global environment for shipping liners.
- OPUS CONTAINER
-
Container Liner Operation Solution
OPUS Container is a maritime container solution that offers efficient management by integrating the entire business in container operations. From shipment booking to its safe arrival at the customer’s destination, it can perform systematic process management through centralized control, which meets global standard work methods and processes.
- CARA
-
Carriers Collaboration Solution
CARA is an integration platform to help enhance communication and cooperation between shipping carriers. None of the shipping carriers supply tonnage and use space autonomously. Every shipping carrier maintains a joint operation and alliance collaboration structure in slot selling/purchase and slot swap by collaboration with other shipping carriers.
- OPUS Bulk
-
Bulk Shipping Solution
OPUS Bulk is a bulk business solution to support small and medium-sized bulk shipping companies’ strategic management and analyze their business results. Bulk shipping companies need to maximize operation efficiency by efficient process management and analysis of shipping data through digital transformation to cope with variability and uncertainty in the bulk business market.
- OPUS Stowage
-
Stowage Planning Solution
OPUS Stowage is a vessel stowage planning solution that aims to provide optimized loading/unloading plan for container shipping companies’ efficient container transportation. It provides stowage data management, including the request for loading work connected to the terminal.
- OPUS DGL
-
Dangerous Goods Management Solution
Managing dangerous goods to prevent possible critical events has been a significant concern in the maritime industry. Safer and systematic management of dangerous goods has been recognized as a primary concern with the increase in shipping transportation and dangerous goods.
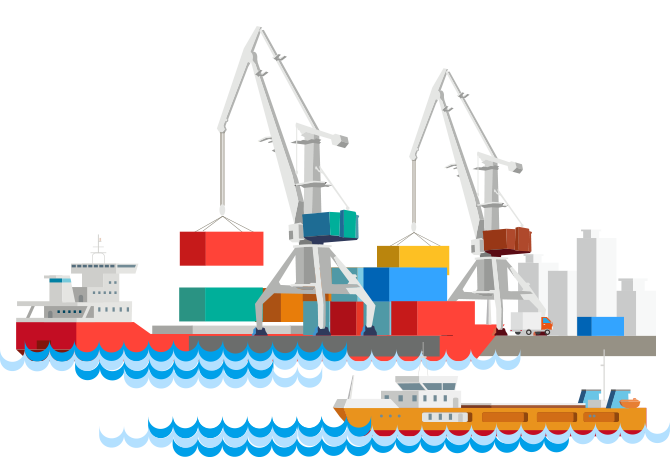
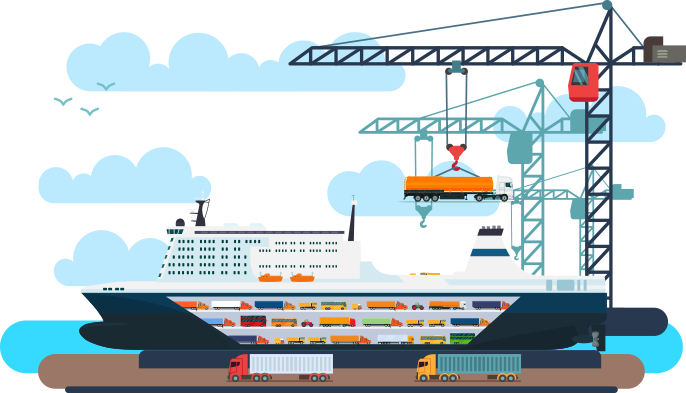

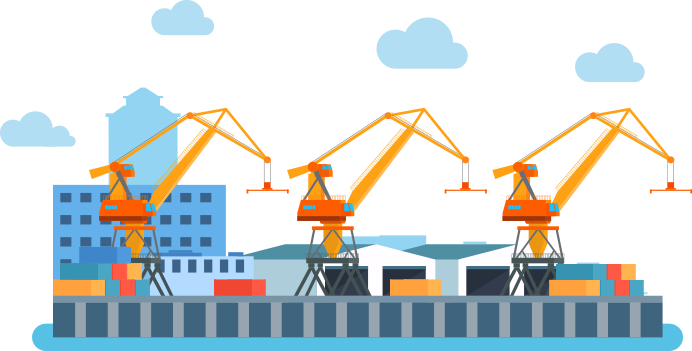
- OPUS Terminal
-
Container Terminal Operation and Decision Support System
OPUS Terminal is a terminal solution that enables the container terminal’s operations including loading and unloading, classification and storage, and flexible responses in newly required terminal works. With constant growth in shipping transportation volume, shipping carriers have responded to increased volume by reinforcing alliances and the enlargement of the vessel.
- OPUS Terminal M
-
Multipurpose Terminal Operation System
OPUS Terminal M is an advanced terminal operating system for multipurpose terminals. (Container, General Cargo, RORO, etc.) OPUS Terminal M is an applicable terminal system for the container, RORO and Bulk, and it is a terminal operation solution applicable for Multipurpose terminals that process the various types of cargo in a single system.
- OPUS DIGIPORT (EAGLE EYE)
-
Digital Twin and Data Analysis Platform
The recent trend of terminal operations is targeted interworking operation between various terminal equipment such as Terminal Operation System(TOS), Gate, External Trucks, Yard Trucks, Yard Cranes, and Quay Cranes for its efficient operation and safety. OPUS Digiport provides 2D & 3D virtual terminal systems based on IoT platform.
- TABS
-
Total Advanced Billing System
TABS is a billing automation solution that offers automated billing tasks for terminals and a 24/7 online service. Terminals throughout the world are making progress from semi-automated to fully-automated operations. Yet the billing work, which calculates the fees, remains complicated to be automated.
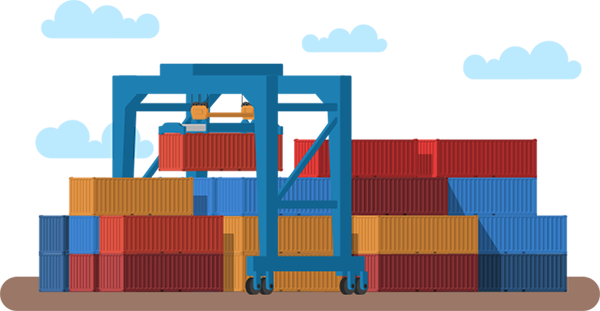
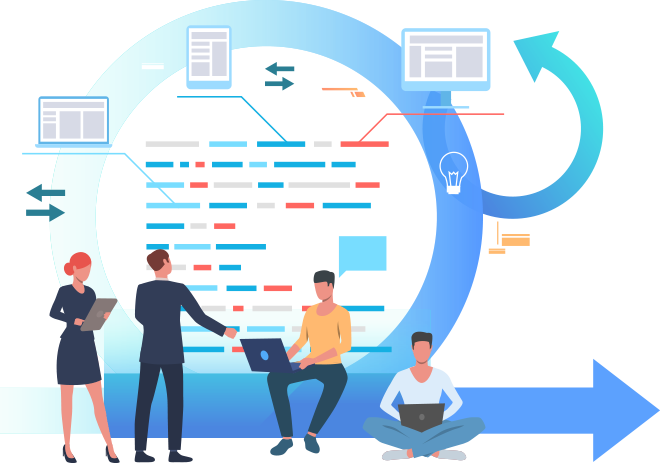
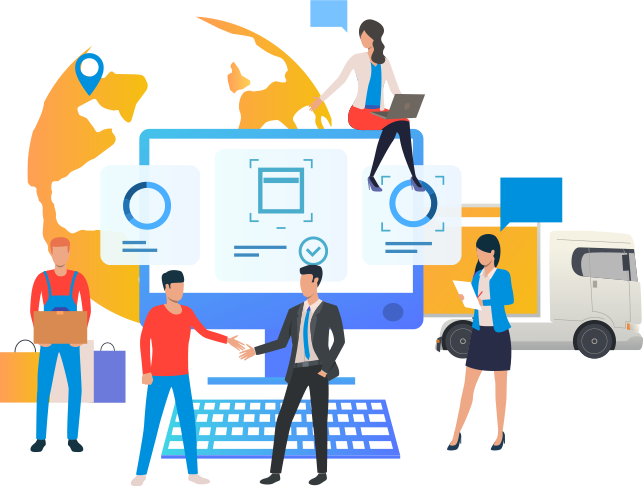
- OPUS D&D
-
Demurrage & Detention Management Solution (SaaS)
OPUS D&D is a solution to automatically calculate demurrage and detention costs based on information about holidays (shipping companies and nations) and tariffs. Over the last few years, demurrage and detention cost reduction has become a significant task for shipping operators due to the decrease in free time and increases in demurrage and detention rates.
- SMARTLINK
-
Data Integration Platform
SmartLink is an iPaaS platform connecting logistics between companies utilizing data and technology. SmartLink started with EDI service in global shipping liners, then SmartLink offers advanced custom declaration in the US per forwarders’ request. Additionally, it extended the various services such as Custom Filling Service, Connection Service between shipping liners and shippers, and Logistics EDI Service.
- CARIS
-
Freight Forwarding & Warehousing Solution
CARIS is a web-based single platform that supports cargo/freight transportation, warehouse management, and global connectivity for Freight Forwarding, NVOCC, and 3PL companies.
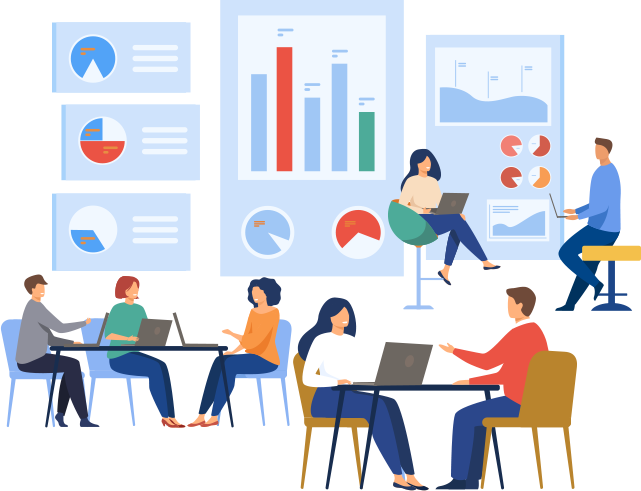
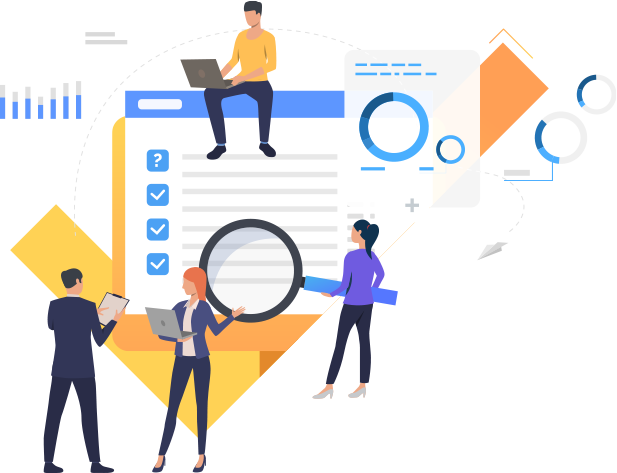
- ODC
-
Offshore Development Service
ODC Service is the service that executes and supports SW development, maintenance, and operation for customers across diverse industries by utilizing the competitive IT manpower in Vietnam. With the universalization of AI, IoT, Metaverse, and the rapid increase of online services, the demand for manpower in SW development is continuously increasing.
- SHINE
-
Positive Outcomes for Logistics Operations
Although many areas have been automated and datafication according to changes in industry, various types of handwritten documents, or documents not unified in the industrial process, still occupy a large portion. SHINE is a solution that offers quick and accurate datafication and its management of the various types of documents created during the initial order and production, procurement and distribution, and customer purchase and service offered in all industrial fields.
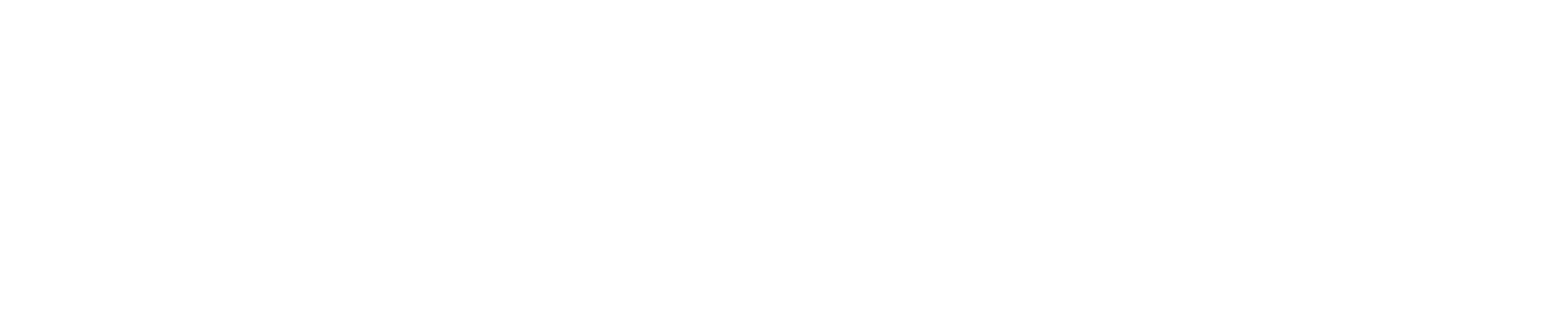
-
MAKING
THE WORLD’S TIME
AND SPACE
MORE VALUABLE
